Plastic cups are becoming a necessary component of contemporary living, being used for everything from big celebrations to regular cold beverages. Gaining knowledge about the complex procedures and technology used in their production might help you better understand these cups. This article will examine the specific procedures involved in making plastic cups, illuminating the equipment, materials, and significance of quality control. We’ll also discuss how top plastic cup manufacturers such as the GMZ company have adopted sustainable techniques to lessen their impact on the environment.
Extrusion: Creating Sheets from Plastic Pellets
Extrusion is the initial process in the production of plastic cups; it involves melting raw plastic pellets and forming them into a continuous sheet. The pellets are first fed into an extruder, a device that melts plastic by heating it to a certain temperature. After that, a die is used to press the molten plastic through to produce a thick sheet. This sheet’s thickness can be changed to accommodate various cup sizes.
For the finished product, the extruded sheet’s quality is essential. For cups that must be strong and long-lasting, thicker sheets are used; for disposable, lightweight cups, thinner sheets are used. Because sheet thickness may be adjusted to suit a range of customer demands, producers can construct a wide range of cups.
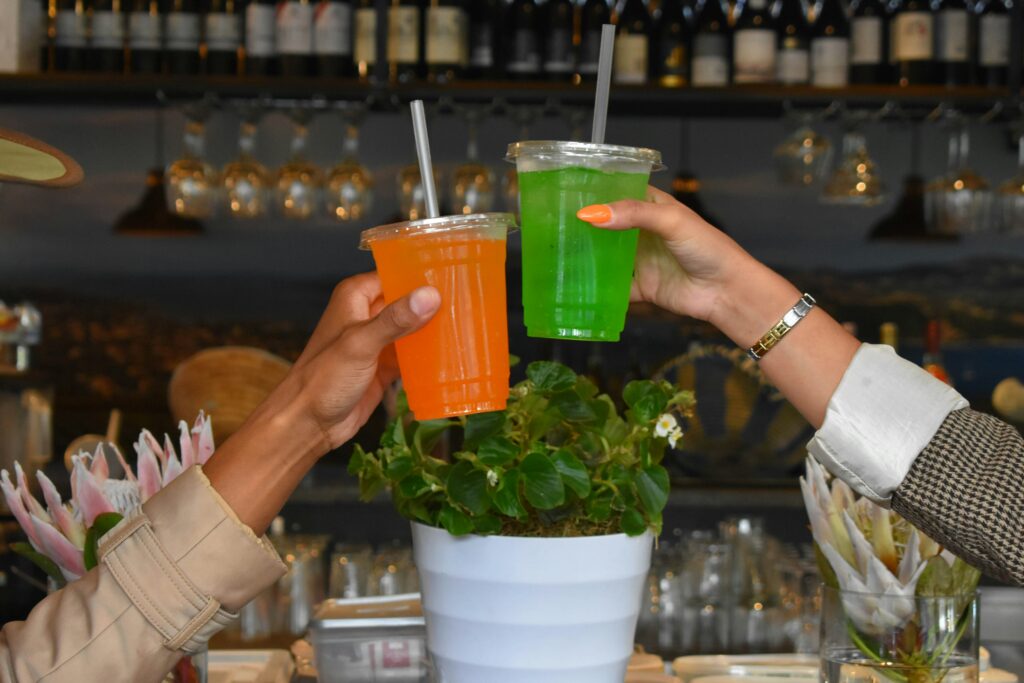
Shape-making using Thermoforming: Plastic Cups
The plastic sheet proceeds to the thermoforming step once it has been extruded. Thermoforming is the process of heating a plastic sheet until it becomes malleable, at which point molds are used to shape it into cups. When thermoforming, there are two primary methods used:
- Vacuum Forming: This process involves placing a heated plastic sheet over a mold and using a vacuum to force the sheet into the shape of the mold. This method is used for high-volume production and works well for making basic cup shapes.
- Pressure Forming: Pressure forming is the process of applying high pressure to push the heated plastic sheet against the mold. This technique is appropriate for producing personalized cups with elaborate patterns or textures as it allows more intricacy and detail in the cup design.
Precision in Cup Cooling and Trimming
To get the right quality, the cups must be chilled and cut after shaping. The cups retain their form and become firmer after cooling. After that, the cups are trimmed to get rid of any extra material and give them a consistent, clean edge.
The usefulness and appearance of the cups depend on precise trimming. It guarantees that the cups are pleasant to handle and use, and it also enhances the end product’s overall quality and beauty.
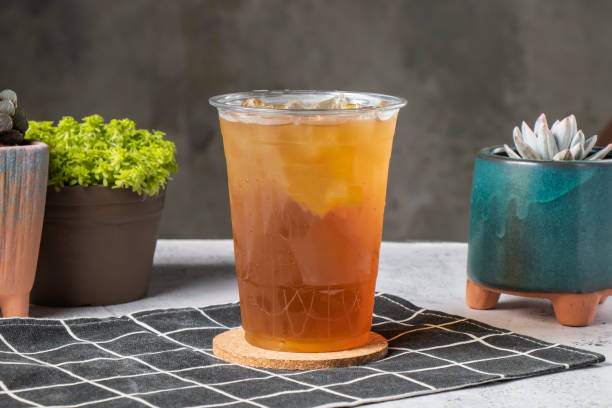
Strict Examinations and Testing
An essential step in the production of plastic cups is quality control. To make sure it satisfies the requirements for strength, durability, and aesthetic appeal, every cup is put through a thorough examination and testing process. Among these checks are:
- Strength Testing: Cups are put through tests to see how well they can handle handling and pressure without cracking or bending.
- Testing for durability entails determining how resistant the cup is to breaking or cracking under typical usage circumstances.
- Aesthetic Inspection: Every cup is examined to look for visual flaws including stained surfaces, jagged edges, or uneven surfaces.
Only cups that pass these exacting tests go to the next level of manufacturing. This dedication to excellence guarantees that customers will obtain dependable and superior products.
Printing on Plastic Cups
A key component of the production of plastic cups is customization, which enables companies to imprint their names, logos, or other designs on the cups. For this, a variety of printing methods are employed:
- Silk screen printing: This technique works well for straightforward patterns with few color options. It offers a strong print that is resistant to handling and cleaning.
- Offset Printing: This method produces detailed, high-quality prints and is appropriate for more intricate designs. It is frequently used on mugs that have complex designs and logos.
- Digital printing is a flexible process that works well for smaller production runs and has fast turnaround times. It is ideal for producing personalized mugs for special occasions or marketing campaigns since it provides excellent design versatility.
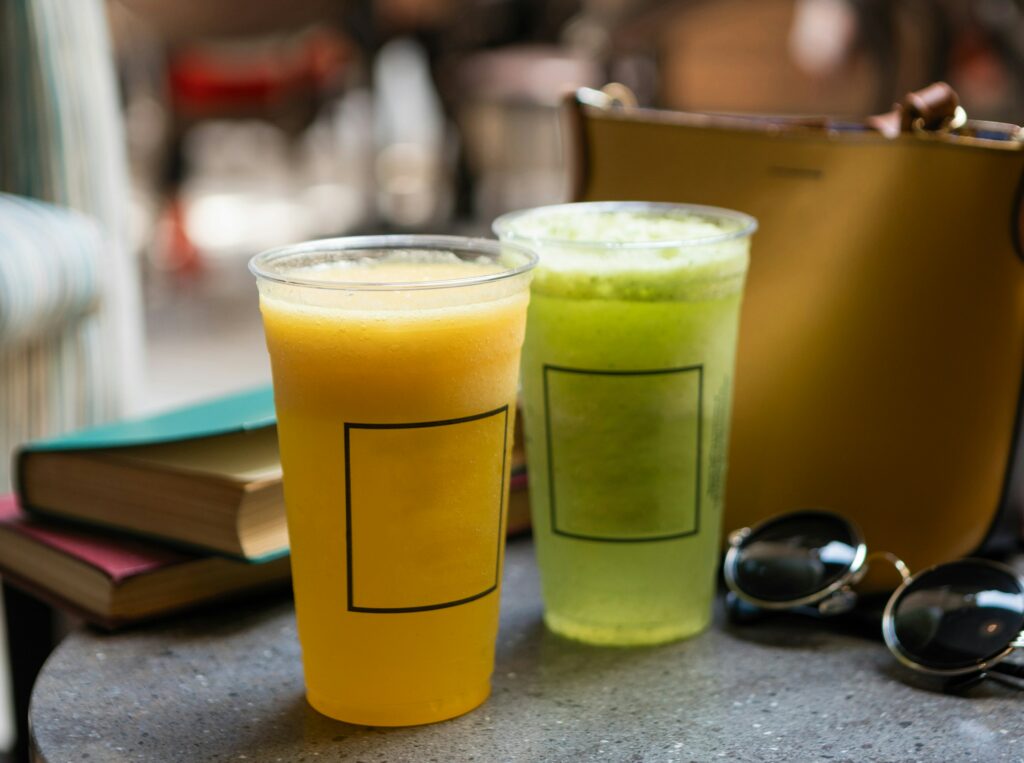
If you’re interested in ordering custom plastic cups with your own logo, consider a company like GMZ. They are known for producing high-quality PET cups with excellent clarity. GMZ offers a variety of cup shapes and sizes, along with customization options that allow businesses to print their logos and designs directly onto the cups. Their commitment to sustainability, innovation, and quality makes them a reliable choice for disposable plastic cups. To order, you typically need to:
- Submit your design file
- Choose your cup size and style
- Specify the quantity needed
- Discuss any specific requirements with their sales team